DMS
ABOUT DMS
Design to Manufacture System (DMS) aims to solve multiple production problems of panel custom furniture enterprises with low cost and high efficiency for small and medium-sized factories. It comprehensively covers the six major links of design, order disassembly, layout, packaging, management, and service, and even small-scale production lines.
DMS SYSTEM PROCESS
Smart Design
One-click CAD
One-click Quotation
Intelligent Document Review
One-click Order Split
Intelligent Scheduling Production
TYPES OF DMS
Solve customer order management issues.
Solve the problem of factory dismantling and reviewing documents.
Solve customer order production problems.
Scan the code to check the status of order and solve the problem of missing boards.
3 TYPES OF INDUSTRY PAIN POINT
Channel development is blocked?
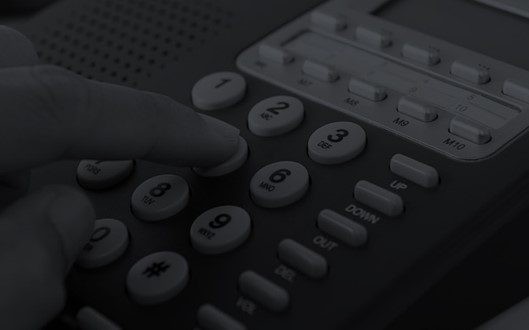
- Is it difficult for dealers to recruit
designers?
- Is it difficult to control the product system?
- Price management module missing?
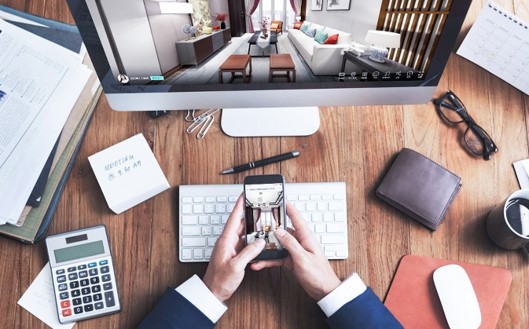
- Lower the threshold for dealers to recruit designers.
- Standardized product system.
- Headquarters standard price system.
Difficulty operating a store?

- Lost customer information?
- Low conversion rate and low unit price per customer?
- Is it difficult to quote or place an order?

- Customer refined management.
- Design to promote sales into large orders.
- One-click quotation, saving people and effort.
Slow production and high cost?

- Is it difficult to dismantle the order?
- Trouble connecting multiple devices?
- High maintenance fees for the front and back end software?
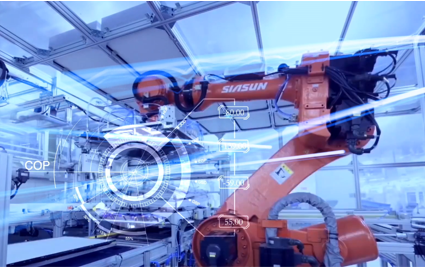
- Receive, review, and dismantle orders by one person.
- Seamless docking equipment, efficient.
- Front-end and back-end share a library maintenance.
DMS CORE ADVANTAGES
01 CRM - Customer Management
Customer Refined Management
Real-time Order Management
Operational Statistics
Reconciliation Inquiries
Comprehensive Income and Expenditure Management
Micro Service
Inventory Management
Mobile CRM
02 DMS - Design Side
Front-end and Back-end Integration
Design Editor
Checking and Splitting Bills
Precise Drawings
03 MSC - Production Docking
Multiple Order Mix
Seamless Docking of Devices
Material Management
Order Scan
DMS IMPROVES OVERALL OPERATIONAL EFFICIENCY
Operation Management
- Real-time tracking of order status.
- Marketing data analysis.
- Multi-channel, multi-mode unified management.
Production Delivery
- Standardize the operation process and reduce manual stickiness.
- Improve production efficiency and shorten delivery time.
- Optimize production scheduling and reduce production costs.
Customer Service
- Improve customer experience and reduce after-sales problems.
- Informatization upgrade to realize standardized management.
- Higher product accuracy and greater customer satisfaction.
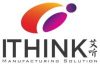
Our Office
No 1 (Tingkat Bawah) Jalan Bestari 1 Taman Bakri Bestari, Bakri Batu 5 Bakri, 84200 Muar, Johor.
TEL : +6017-588 9668
EMAIL : ithink.mfgsoln@gmail.com